What is a Gap Analysis?
This article describes what a gap analysis is in the context of managing your quality system when standards and regulations are updated.
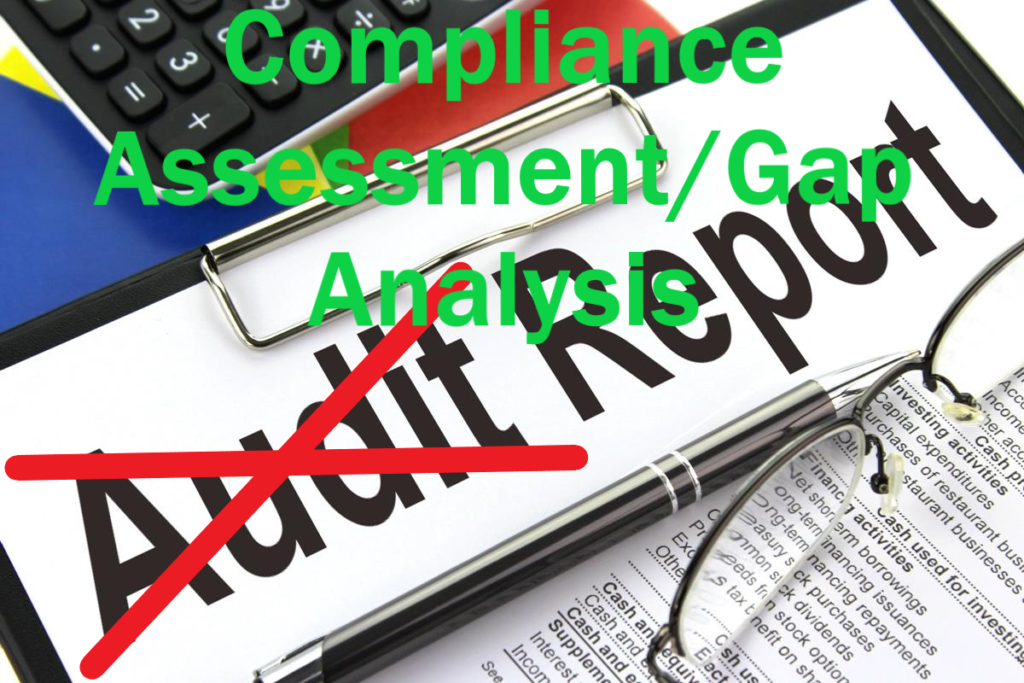
What is a Gap Analysis? An introductory look.
Well, that depends on the context. The dictionary definition is “A technique that businesses use to determine what steps need to be taken in order to move from its current state to its desired, future state. Also called need-gap analysis, needs analysis, and needs assessment.”
For the most part, this is correct, but we need to tweak it just a little bit to fit better into our regulatory affairs niche, specifically medical device manufacturers. A gap analysis for financial investment or an advertising firm will be very different than one for a medical device distributor. It might even be better served to be called a compliance assessment/gap analysis, but I am sure someone else has thought of that long before me.
For our purposes, the gap analysis is a formal comparative review of an internal process or procedure against a standard, good practice, law, regulation, etc. This blog article will be an introductory look into that process. We also created a procedure case study that shows how a gap analysis can be used to review your management procedure against the requirements in ISO 13485:2016.
What are the two BIG goals of a Gap Analysis?
It sounds like a simple exercise, but the gap analysis or “GA” for short can have two very different but complementary functions. Rather than simply hunting for areas of non-compliance, the first goal is to find and demonstrate areas of compliance.
The second more obvious goal is to find the gaps between the process and the regulatory requirements they are being compared against.
Why is demonstrating compliance important?
Because this is a formal documented review, a gap analysis provides documentation in a traceable manner of meeting the requirements that have been laid out. That traceability is important because it allows anyone to read the report, see the requirement, and locate the area of the procedure that demonstrates conformity with that requirement.
The report itself is an objective tool, not something that is meant to be a witch hunt. The gap analysis will compare document contents. If you want to verify that the entire process is fully compliant, you will need to dig deeper and observe if the activities laid out within the procedure are being performed per the procedure instructions. It is possible to draft procedures that are compliant with text requirements but non-compliant in the manner that the actions are being performed and documented.
What about gaps?
The gaps, or areas of non-compliance highlight opportunities for improvement, if there are any. A gap assessment may not find any gaps and present a report that clearly and neatly outlines and explains how each regulatory requirement is being met.
If there are any gaps identified, that does not mean that there is cause for concern. This should be viewed instead as an opportunity for improvement. Standards and procedures change over time, and, naturally, procedures and processes will have to change with them.
The very act of the gap analysis shows that there is a documented effort towards continual improvement as long as the gaps are addressed.
Addressing the Gaps
The report is ideally the first and last step, and you have a wonderful piece of paper to show that someone checked, and all of the required areas are being met. However, this is not always the case. When there are gaps, they must be filled.
Addressing a gap should happen in a traceable manner, one that shows it was identified, acknowledged, and then how it was fixed. Something that might be addressed through your CAPA process, but that is a topic for a different time.
In Closing
The compliance assessment/gap analysis is a singular tool used in the overall maintenance of a quality system. Its actions and performance are similar to a simplified type of audit, but the gap analysis itself is not going to replace your regularly scheduled audit activities. However, it will help you monitor and keep your fingers on the overall pulse of your quality system. This is also especially helpful in situations where standards and regulations are updated, and your quality system needs to be evaluated and updated accordingly.
For more in-depth education in specialized areas of the assessment, look into our training on Technical File Auditing for MDR compliance against Regulation (EU) 2017/745 at the link below.
https://medicaldeviceacademy.com/technical-file-auditing/
What is a Gap Analysis? Read More »