This blog revies some practical and effective management skills that all managers should possess.
Sometimes we hear phrases like: “Well, that’s just an ISO requirement.” This apparent lack of support by top management is what frustrates every Management Representative in the world.
Peer Support
For a Quality Manager or any manager, it is vital to gain support from our peers, as failure to do so can lead to challenges. While the Quality Department plays a crucial role in recommending improvements, providing training, and assisting with implementation, it cannot address all problems on its own. Therefore, I strongly believe in assigning corrective actions to the process owner (i.e., the Manager) responsible for the area where the problems originated. This approach creates an opportunity for QA/RA to collaborate with the area manager and work together as a team towards the shared goal of improvement.
Good managers build people up and improve processes, they don’t point fingers or blame individuals. It is the process, not the person.
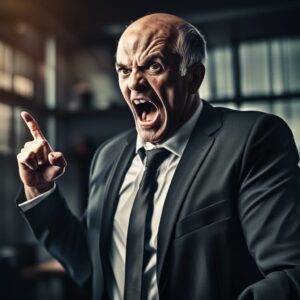
Persuading Skeptics
If you encounter resistance when trying to persuade skeptics, focus on a crucial project for the individual opposing your ideas. Demonstrate how applying Quality principles can effectively resolve their problems, potentially gaining their support. Converting one person often leads to strong support from them. If the resistant individual holds a senior position such as the CEO, take time to understand the CEO’s initiatives (These shouldn’t be hard to identify as they likely talk about them rather constantly). Illustrate how their actions can align with Quality Objectives, using graphs and presenting well-thought-out solutions to their challenges. Utilize the CAPA (Corrective and Preventive Action) process as a framework to show how the management team can collaboratively address issues.
If nothing seems to be working, you can always try reviewing some FDA MedWatch reports too–just to scare your boss.
Here is a list of tips to deal with unsupportive top management in a quality management system using effective management skills:
Clearly communicate the benefits of the quality management system:
Articulate the advantages that a well-implemented quality management system can bring to the organization, such as improved efficiency, reduced costs, and enhanced customer satisfaction. Don’t just leave the conversation at “The QSR/13485 says that we SHALL have one”.
Address specific concerns and show how quality initiatives overcome challenges:
Listen to the concerns of top management and present how quality initiatives directly address those issues, fostering a more positive outlook towards the system. Just like the old saying,
“An ounce of prevention is worth more than a pound of the cure”
Consider how ISO 13485:2016 has separate sub-clauses for Corrective Actions and Preventive Actions. Explain how something like pushing for preventive actions shows compliance with clause 8.5.3. which auditors, and inspectors will be looking for, but also that every Preventive Action represents a dodged 483 letter or recall.
Or how beefing up incoming inspection is likely to save time and money in reworked product and less scrap dispositions because any non-conforming materials are stopped before they can make their way into finished devices.
Demonstrate how quality aligns with overall business objectives:
Connect the quality management system to the organization’s strategic goals, highlighting how it contributes to long-term success and profitability. Reframe the Quality Policy and Quality Objectives as tools to support a successful business. Not just, “We have to have them for compliance….”
Start with small projects and showcase measurable results:
Begin with pilot projects or smaller initiatives that demonstrate tangible improvements, instilling confidence and support from top management.
Create a compelling business case for the quality management system:
Develop a well-researched and data-driven business case that outlines the return on investment and the long-term benefits of implementing the system. Effective management skills will involve encorporating topics like regulatory compliance. Not only how they align with, but are a part of business goals.
Involve top management in decision-making related to quality:
Engage top management in the decision-making process. Seeking their input and making them feel invested in shaping the quality management system. It is important that the entire organization be ‘quality focused’ at all times. Not just when an audit or management review is approaching.
Consider the potential consequences of non-compliance with quality standards:
Emphasize the impact of not adhering to quality standards, such as regulatory penalties or reputational damage. This will underscore the necessity of the system’s implementation. This can be validated externally if need be. Auditors or consultants can assess quality processes and provide independent validation of a systems strengths of weaknesses.
Pingback: Effective Management Solutions for 10 CAPA Program Blunders - Medical Device Academy Medical Device Academy